How to Calculate the RPM of a Motor
RPM Calculator
RPM |
Working Principle of Electric Motors
An electric motor is a device that transforms electrical energy into mechanical energy. Electric motors are used in a variety of industrial applications, to provide mechanical energy to run power tools, fans, electric vehicles, etc. These motors operate on the basis of the electromagnetism principle, which states that: if a current-carrying conductor is placed in a magnetic field, it experiences a mechanical force caused by the attractive and repulsive forces created by the magnetic field. The magnitude of the mechanical force may be obtained as a product of the magnetic field, the current in the conductor, and the length of the coil in the motor. While the direction of motion of the conductor can be determined by Flemings left-hand rule.
Generally, electric motors consist of three main parts namely: the stator, rotor, and commutator; though the motor designs may vary depending on the manufacturer and the application of the motor. The stator is the stationary part of the motor and in most cases, it is a permanent magnet or a row of magnets lining up the edge of the motor casing. The rotor/armature is the rotating part, and is placed inside the stator. The rotor consists of copper wires wound into a coil around an axle or the motor shaft. When current flows through the copper wires, it creates a magnetic field that interacts with the field generated by the stator, causing the axle (motor shaft) to spin.
The commutator is a metal ring which is divided into two halves. It is attached to one end of the coil. Its main function is to reverse the direction of the current in the armature whenever the coil rotates by half a turn. This helps to ensure that the ends of the coil do not move in opposite directions, enabling the motor shaft to spin in only one direction.
The three parts of the motor (stator, rotor, and commutator) rely on the repulsive and attractive forces of electromagnetism, which cause the motor shaft to rotate continuously whenever a steady current is supplied to it. The magnetic poles of the armature try to line up with the opposite magnetic poles of the stator, opposite poles attract while the same pole repels.
There are two broad classifications of electric motors: DC and AC motors. The main difference between them is that DC motors operate on Direct Current (DC) while AC motors operate on Alternating Current (AC). Each of these types of motors has diverse characteristics in terms of performance, reliability, efficiency, and cost.
However, one of the most important parameters considered when selecting or determining the performance of any of the two types of motors is the motor RPM. Understanding the basics of the motor RPM is essential, as this knowledge will assist you to select the right type of motor for your specific application; by determining the motor output torque and motor speed. Also, knowing how to calculate the RPM of a motor, can assist you to effectively monitor and control the motor's operation. Overall, regulation of motor RPM plays a key role in industrial processes that use motors for constant and variable speed control as well as torque control.
What is the RPM of an Electric Motor?
RPM is a short-form of Revolutions Per Minute (RPM). It is a unit of rotational/ angular speed that indicates the rate of revolution of the rotor component i.e., the number of full rotations the rotor makes per minute. Simply, RPM is a measure used to describe the rotational speed of the motor's spindle/motor shaft.
The RPM of an AC motor is dependent on two main factors: the frequency of the supply power line, and the motor wiring, specifically the number of poles. On the other hand, the rpm of a DC motor is influenced by the operating voltage, the strength of the magnetic flux linkage, and the number of turns on the armature. Therefore, to achieve the desired output speed, you must operate an AC motor within the specified range of line frequency, and in case you have a DC motor, you should operate it within the recommended voltage values.
An AC voltage supply line may have a frequency of 50Hz or 60 Hz depending on the national-grid frequency of a given country. In a 60 Hz power supply, the polarity of the motor's armature shifts faster compared to a 50 Hz power supply. Hence, a motor rated at 50Hz will have a higher rotational speed compared to one rated at 60Hz. Higher RPM leads to higher shaft power, more reactive current, and thus low power factor. Even though a higher RPM makes a motor generate more heat, the cooling fan will also be running at an equally higher speed; thereby dissipating the extra heat at a faster rate. Connecting a 60Hz motor to a 50Hz power supply has no major effects, only that the motor will operate at about 83% of its rated speed.
However, if you vary the motor's RPM at a different voltage value than the rated operational voltage of that specific motor, a saturation of its magnetic core is likely to occur. Magnetic core saturation causes a drastic increase in current draw, which in turn makes the motor unit overheat. You can prevent magnetic core saturation by reducing the input voltage and maintaining a constant voltage to frequency ratio.
Calculating the RPM of a Motor
Mathematically, the motor speed can be expressed as a function of the frequency of the supply voltage and the number of poles on the motor, as follows:

For AC motors, three types of motor RPM can be calculated i.e., the no-load RPM, RPM slip, and full-load RPM. To obtain the no-load RPM, you multiply the line frequency by 60 and then by two and finally divide the results by the number of poles in the motor. The 60 in the multiplication represents the number of seconds in a minute and the essence of multiplying by 2 is because there are negative and positive pulses in a power cycle.

The actual motor RPM is always lower than the synchronous speed. This is because if the armature rotates at the given synchronous speed, the stator windings magnetic field would no longer interact with the magnetic field of the rotor windings i.e., there will be no relative motion between the two magnetic fields. In such circumstances, it means that zero current will be inducted into the rotor windings and therefore no magnetic field would be generated in the armature to cause it to turn. The difference between the motor's synchronous speed and the actual speed is called the RPM slip, mathematically expressed as:

It can also be obtained by converting the motor slip rating to RPM as follows;

To evaluate the motor slip rating you first find the difference between the synchronous speed and the rated full load speed and then divide the results by the synchronous speed and multiply the answer by 100%, mathematically expressed as:

The full load RPM is obtained by subtracting the RPM slip from the no-load RPM.

For the DC motors, the RPM depends mainly on the input voltage to the motor. Mostly, the DC motor manufacturers provide a chart showing the expected motor speed at various voltage settings. To obtain the desired RPM, one can regulate the input voltage according to the chart.
Examples of Motor RPM Calculations
We will consider some examples of calculating the RPM of a motor. As previously shown, for AC motors, the no-load RPM is a function of the line frequency and the number of poles.
Example 1: Given a line supply frequency of 60Hz and an AC motor with four poles, the no-load RPM of the motor can be determined as:

The amount of slip varies from one motor to another depending on the motor construction. For example, if the actual RPM of the motor indicated on the nameplate of this motor is 1725 rpm, the RPM slip would be.

If an RPM slip of 75 rpm is given for a 60Hz and 4-pole motor, the full load rpm rating for the motor would be:

Example 2: For a 60Hz motor with two poles and an RPM slip of 150 rpm, determine the no-load and full-load operating speed.
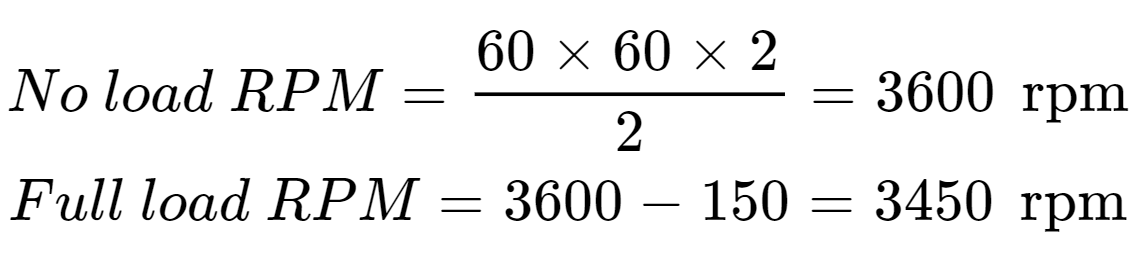
Conceptually, a 6 poles electric motor connected to a 60 Hz power supply operates at an unloaded speed of 1200 rpm and a loaded speed of 1175 rpm. While an 8 poles motor would have an unloaded speed of about 900 rpm, and 800 rpm when loaded. The most common AC motors are 2-pole, 4-pole, 6-pole, and 8 pole motors. 12 and 16-pole motors deliver an unloaded operating speed of 600 rpm and 450 rpm respectively, but they are less common.
Regulating the RPM of an AC Motor
The synchronous speed of an AC induction motor can be regulated using a variable frequency drive. A variable frequency drive can help with altering the frequency of the stator because it would spin at the same frequency as that of the rotating magnetic field of the AC power supply. The synchronous speed can be expressed as a function of the stator frequency and the number of poles,
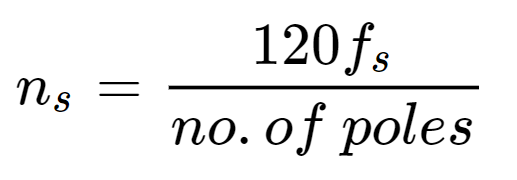
Where;

Thus, if a synchronous speed of 1500 RPM is desired for an AC induction motor with 4 poles, then required stator frequency would be:
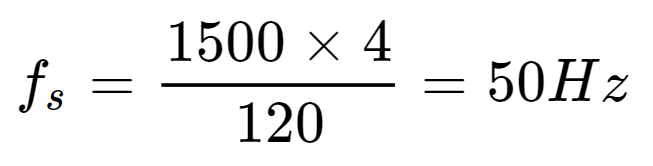
Also, the wiring design determines the number of poles in the motor, and increasing the number of poles on the motor decreases the no-load and full-load operating motor RPM. Particularly, the number of poles affects the motor speed in that, increasing the number of poles causes the motor to run much slower. For instance, the armature of a two-pole motor will achieve a complete 360-degree rotation with just a single polarity change while the armature of a four-pole motor will only achieve a 180-degree rotation in a single polarity change.
Therefore, if you were to keep all the other parameters constant, the RPM of a 2-pole motor would be twice that of a 4-pole motor. And since the polarity of a 60Hz power supply changes 60 times every second. A 2-pole motor connected to such a power supply (60Hz) would rotate at 3600 rpm and a 4-pole motor would record a rotational speed of 1800 rpm.
Why is it Important to Calculate Motor RPM?
When operating, repairing, or even replacing a motor it is crucial that you fully understand the motor's specifications. As previously mentioned, calculating the motor RPM is one of the key factors considered during motor selection. As the accurate calculation of the motor RPM can readily assist you to evaluate the rotational mechanical power of the motor shaft, which is fundamental in determining the capability of a given motor to perform a specific task.
The knowledge of motor RPM is also crucial when electrical and design engineers are developing graphical illustrations for motor characteristics using torque-speed curves. The reason being, to construct the toque-speed curves you need to plot the motor RPM, armature current, mechanical power output, and efficiency as functions of the motor output torque. The torque-speed curves are very common in technical guides for DC motors, as they provide guidance on how you can regulate the RPM of your DC motor.
When motor manufacturers are specifying the back EMF (back electromotive force) of a motor, they require the angular speed of that motor. Also known as counter EMF(CEMF), back EMF is the voltage that occurs when the armature is rotating, and it is directly proportional to the angular velocity of the motor. The constant of proportionality in that relationship is referred to as the "back EMF constant" of the motor, often stated in units of volts/rpm. Therefore, given the value of the back EMF constant, you can evaluate the motor speed in compatible units i.e., RPM can be used to calculate the expected value of the back EMF of the motor.
The motor RPM also helps to determine the amount of power output from the motor. At zero rpm, the power output is zero and at maximum operating speed (RPM) the value of the motor's power output is at its highest. The torque or the driving force which causes a motor to run is also active from 0% to 100% operating speed. The motor torque is relatively constant throughout the motor operation, but the motor delivers higher output power at a higher speed. This means that a motor will have higher power output at higher RPM settings and it will have low power output at lower rpm settings. Mathematically,
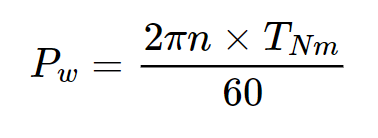
Where;
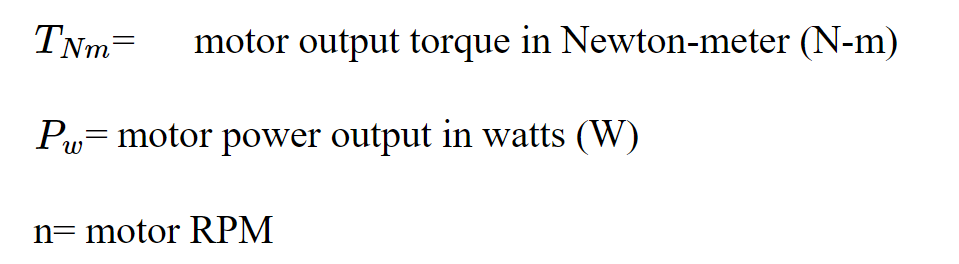
For example, given an electric motor that delivers an output torque of 3.6Nm at a speed of 2000 RPM, the shaft power output of the motor would be:

If the motor speed settings of the same motor were to be changed to 3450 rpm, then the motor would produce an output power of 1.3 kW. Therefore, the knowledge of motor RPM will always help to maneuver across the motor settings to achieve the desired motor performance in terms of torque and power output.
Conclusion
The motor RPM is one of the most important factors that influence the performance of either AC or DC motors. Calculating the motor RPM accurately is especially significant when selecting a motor for a given application, or when repairing and replacing an old motor. This article guides you on how to calculate the no-load, full load, and slip RPMs of AC motors. It also guides you on how to regulate the RPM of both AC and DC motors. For more information or to discuss which equipment might be best for your application, please visit our website here, or contact us at sales@dosupply.com or 1-800-730-0292.
No comments:
Post a Comment
Thank you for Contacting Us.