Computer Aided Process
Planning
Computer Aided Process Planning (CAPP)
…..Process planning with the aid of computer
• Process planning is concerned with the preparation of route sheets that list the sequence of operations and work centers require to produce the product and its components.
• Manufacturing firms try to automate the task of process planning using CAPP systems due to many limitations of manual process planning. These includes:
– Tied to personal experience
– and knowledge of planner of production facilities, equipment, their capabilities, process and tooling. This results in inconsistent plans.
– Manual process planning is time consuming and slow.
– Slow in responding to changes in product design and production.
• The experience of manufacturing of different engineers, who are likely to retire, can be made available in future by CAPP.
• CAPP is usually considered to be part of CAM, however this results CAM as stand alone system.
• Synergy of CAM can be achieved by integrating it with CAD system and CAPP acts as a connection between the two.
• Readymade CAPP systems are available today to prepare route sheets.
CAPP
Computer Aided Design (CAD)
Computer Aided Manufacturing (CAM)
Synergy results in when CAM is integrated with CAD to form CAD/CAM systems than a stand alone CAD or CAM systems. In such a system CAPP becomes a direct connection between design and manufacturing
Benefits derived from CAPP
• Process rationalization and standardization
• Increased productivity of process planners
• Reduced lead time for process planning
• Improved legibility
• Incorporation of other application programs
CAPP Model
CAD system
Preprocessor
Knowledge
Input Output
CAPP Model
Planning rules
Postprocessor
CAPP System Architecture
CAD System Preprocessor
Machining Knowledge base
Machining selection module
Constraint application module
Constraint Creation module
Manufacturing knowledge base
Design approaches of CAPP systems
Retrieval CAPP systems/ Variant CAPP
– This has evolved out of the traditional manual process planning method. A process plan for a new part is created by identifying and retrieving an existing plan for a similar part, followed by the necessary modifications to adapt it to the new part.
– It is based on GT principles, i.e., part classification and coding. These coding allow the CAPP system to select a baseline process plan for the part family and accomplish about 90% of the planning work. The planner adds the remaining 10% of the planning by modifying the baseline plan.
– If the code of the part does not match with the codes stored in the database, a new process plan must be generated manually and then entered into database to create a new baseline process plan for future use.
Advantages and limitations of Variant CAPP
– Investment in hardware and software is not much.
– The system offers a shorter development time and lower manpower consumption to develop process plan.
– The system is very reliable and reasonable in real production environments for small and medium size companies.
– Quality of process plan depends on knowledge and background of process planner.
Generative CAPP
• Process plans are generated by means of decision logics, formulas, algorithms, and geometry based data that are built or fed as input to the system.
• Format of input
– Text input (interactive)
– Graphical input (from CAD models)
• First key: to develop decision rules appropriate for the part to be processed. These rules are specified using decision trees, logical statements, such as if-then-else, or artificial intelligence approaches with object oriented programming.
• Second key: Finding out the data related to part to drive the planning. Simple forms of generative CAPP systems may be driven by GT codes.
• A pure generative system can produce a complete process plan from part classification and other design data which does not require any further modification or manual interaction.
• In generating such plans, initial state of the part (stock) must be defined in order to reach the final state i.e., finished part.
• Forward or backward planning can be done.
• Forward and backward planning apparently appear to be similar but they effect programming significantly. The requirement and the results in of a setup in forward planning are the results and requirements , respectively, of the set up in backward planning.
• Forward planning suffers from conditioning problems; the results of a setup affects the next set up.
• In backward planning, conditioning problems are eliminated because setups are selected to satisfy the initial requirements only.
• The generative CAPP has all the advantages of variant CAPP however it has an additional advantage that it is fully automatic and a up-to-date process plan is generated at each time.
• It requires major revisions if a new equipment or processing capabilities became available.
• The development of the system in the beginning is a difficult
Thursday, 27 August 2020
Home
A Practical Guide for Mechanical Engineers
CAD
cad cam
CAD MEP HVAC ANSYS
CAM
CAPP
What is computer aided process and planning
What is computer aided process and planning
Tags
# A Practical Guide for Mechanical Engineers
# CAD
# cad cam
# CAD MEP HVAC ANSYS
# CAM
# CAPP
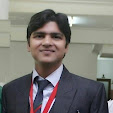
About Devendra Singh
CAPP
Subscribe to:
Post Comments (Atom)
Post Top Ad
Author Details
Home Teacher India, founded by Devendra Singh in 2013. He completed his Master's in Technology from National Institute of Technology, Durgapur. He believe's Education is a birth right for all, so he established HTI, to provide free education and technical support to needy students form all specializations and reach them with our service.
It is a non-profit organization aims to spread the light of knowledge and skills to all who needs.
No comments:
Post a Comment
Thank you for Contacting Us.